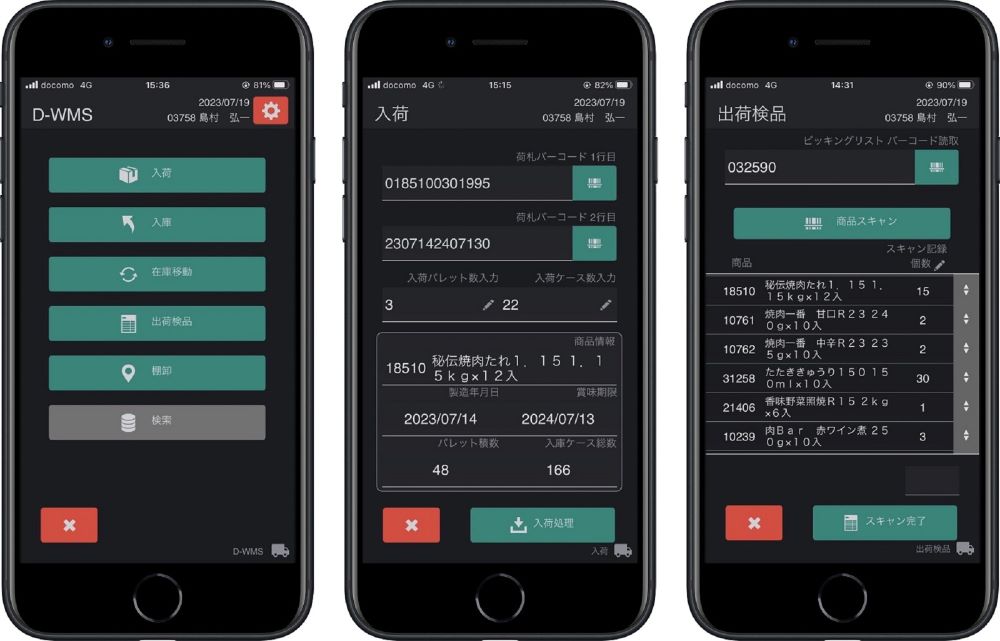
20 年使った倉庫管理システム、数千万円と 1 年をかけてリプレース?
「おいしさで・しあわせをつくる」を企業理念に、焼肉のたれや鍋用スープ、味・塩こしょうなど、調味料を中心に日本の食卓においしさを提供し続けている株式会社ダイショー[証券コード:2816]。同社は 2005 年から、Apple 子会社 Claris International が提供する Claris FileMaker を活用し、食品安全の取り組みを支える「生産管理システム」をアジャイル開発で構築。品質向上と効率化を両立しながら、食品の安全を実現してきた。
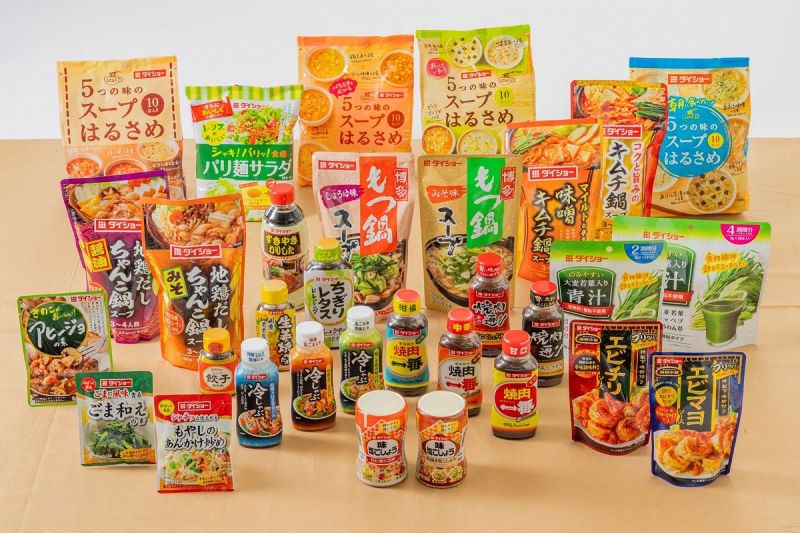
同社は福岡県と茨城県に 食品安全認証規格(FSSC22000)を取得した計 4 つの工場を持ち、「焼肉のたれ」、「博多もつ鍋スープ」、「キムチ鍋スープ」をはじめとした調味料などの商品を全国に届けている。茨城県小美玉市にある関東工場に隣接する浅美倉庫は、東日本を中心とする商品出荷の拠点となっており、東日本のスーパーマーケットや食品加工会社などに商品を届けている。
関東工場で生産された商品と九州工場から送られてきた商品を保管・出荷するという物流業務を支える倉庫管理システムは、2002 年から使用されていた。使用開始から 20 年が経つ頃には、ベースとなる OS の更新対応や、ハンディターミナルなどのハードウェアの調達の難しさや、ソフトウェアの使い勝手の悪さなどの問題が出てきており、システムのリプレースが必要になっていた。
当時のシステムは外部のシステムベンダーによるスクラッチ開発で、細かな業務プロセスの変更に対応するという柔軟な変更ができなかった。例えば納入先から送り状に賞味期限を記入するように求められても、システムを簡単に修正できないため、現場で手書きで記入していた。また、倉庫内では専用のハンディターミナル(バーコードなどを読み取りデータを収集する携帯用端末)で入力作業を行っていたが、事務所に戻ってクレードル(通信・充電ができるハンディターミナル用のデッキ)に差し込まないとデータが送受信されないため、入荷、入庫、在庫移動、出荷といった業務を並行して行うことができず、効率が悪かった。さらに、システムの修正が難しいがゆえに、なかなか新たな取り組みができないという課題もあった。株式会社ダイショー 物流部 課長代理 清水 良之 氏は、「以前から複数の企業が同じ届け先の荷物を混載して配送する、共同配送に取り組みたいと思っていました。しかし、そのためにはシステム改修が必要で、これまで挑戦できずにいました」と語る。
そこで物流システムのリプレースを検討。システムベンダーからは数千万円程度の費用で、完成まで約 1 年かかると言われていた。
ハンディターミナルよりも iPhone を導入することで DX を加速できる
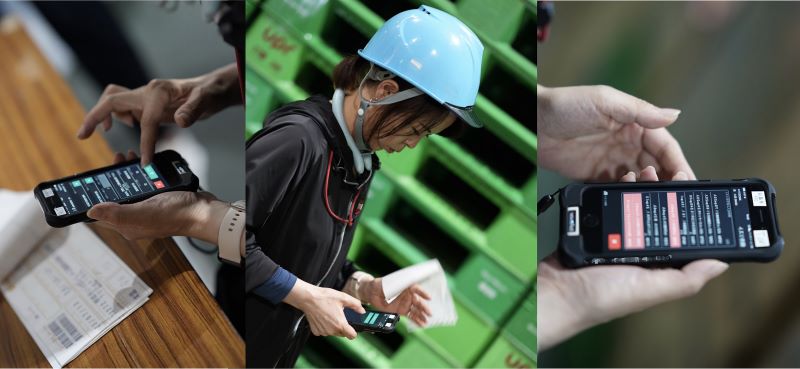
ハンディターミナルに代わり導入された iPhone と 内製アプリ D-WMS
ちょうどその頃、同社 執行役員 経営企画室長 三浦 和信 氏が、物流部の担当執行役員も兼務することとなった。三浦氏は生産管理部門で FileMaker を活用した生産管理システムの開発を主導した経験があった。生産管理システムで大きな手応えを感じていた三浦氏は、倉庫管理システムについても、FileMaker によるシステムの内製化を検討する。三浦氏は、「以前から FileMaker と iPhone や iPad を連携させて使ってみたいと考えていました。当時使っていたハンディターミナルはちょうどスマートフォンのような形状で、これなら iPhone が使えるのではないかと思ったのがきっかけです。物の出入りを管理する倉庫システムは、おおむね足し算と引き算でこと足ります。2 か月もあればできるだろうと考えました」と説明する。また、経営企画室 部長代理 松井 伸明 氏は、 iPhone を活用することについて、「 iPhone なら情報共有など別の業務に活用したり、倉庫管理システム以外の使い方が可能です。それに比べて専用のハンディターミナルは高額なうえ、その目的にしか使えません。今後の拡張性と FileMaker との親和性を考えると、デバイスは iPhone が最適と考えました」と語る。
FileMaker を使ったアジャイル開発なら 1/10 以下の費用で導入が可能
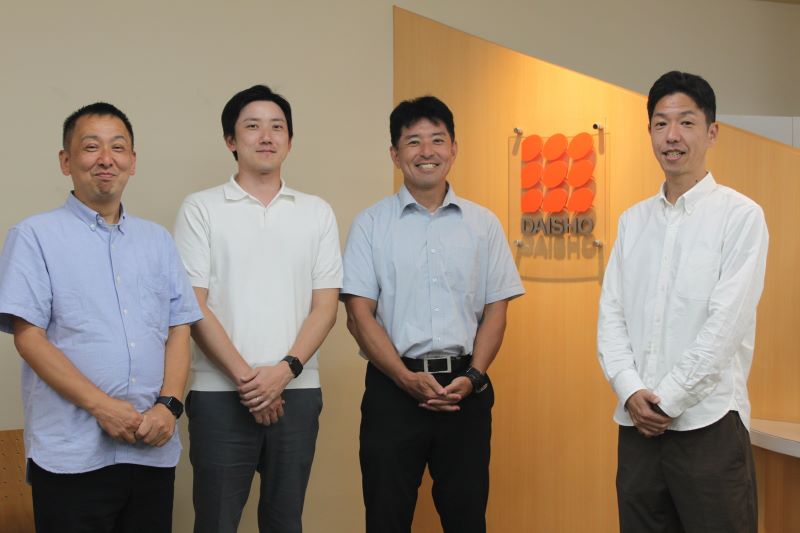
ダイショー本社 左から:三浦 和信 氏(執行役員 経営企画室長)、松本 俊一 氏(取締役副社長)、加藤 成隆 氏(情報システム部 係長)、松井 伸明 氏(経営企画室 部長代理)
これまで FileMaker を使ったシステム開発は情報システム部門主導ではなく、部門ごとに現場主導で行われていた。しかし、今回は在庫管理データを扱うため、基幹システムと Claris FileMaker Server の双方向に通信する作業も発生する。そのため、ユーザである物流部と、FileMaker の知見を持った経営企画室、基幹システムを管理する情報システム部の 3 部門合同でアジャイル開発プロジェクトを発足。同社の取締役副社長 松本 俊一 氏がそのプロジェクトのトップに立つこととなった。松本氏は、
「ダイショー全体としても、DX に取り組む必要性を感じていたこともあり、システムの内製化を推進することは良いことだと引き受けました。元々数千万円のコストと 1 年の期間がかかると考えていたシステムが、10 分の 1 以下の予算と数か月で導入できるなら、会社としてこんなありがたいことはありません」と語っている。
プロジェクトは 2022 年 9 月にスタート。まず三浦氏と松井氏が講師となって、松本氏を含むプロジェクトメンバーに対し FileMaker の講習を行った。講習を受けて、「私も簡単なデータベースを作れるようになりました」(松本氏)。10 月にはシステムの全体構成が決定し、松井氏が中心となって開発をスタートした。2023 年 2 月ごろには一旦完成し、現場での検証を開始。必要に応じて修正を加えながら、3 月 1 日から実運用を開始した。1 か月程度、現場の要望を聞きながら修正を行い、6 月には出荷検品機能を追加でリリースした。
実際にかかった開発期間は約 4 か月、10 分の 1 と言われた導入費用の多くは、iPhone 導入と外付けのバーコードリーダー(AsReader)にかかわるハードウェア費用であった。
一方、これまで既存の倉庫管理システムを管理していた同社の情報システム部 係長 加藤 成隆 氏は、「最初に計画を聞いたときは本当に数か月でできるのかと驚きましたが、実際、システムを本格的に組み始めてから 1 か月後にはかなりできあがっていたので、これなら短期間で実現できそうだと思いました」と語る。
入出荷の正確性が格段に向上し、効率化も実現
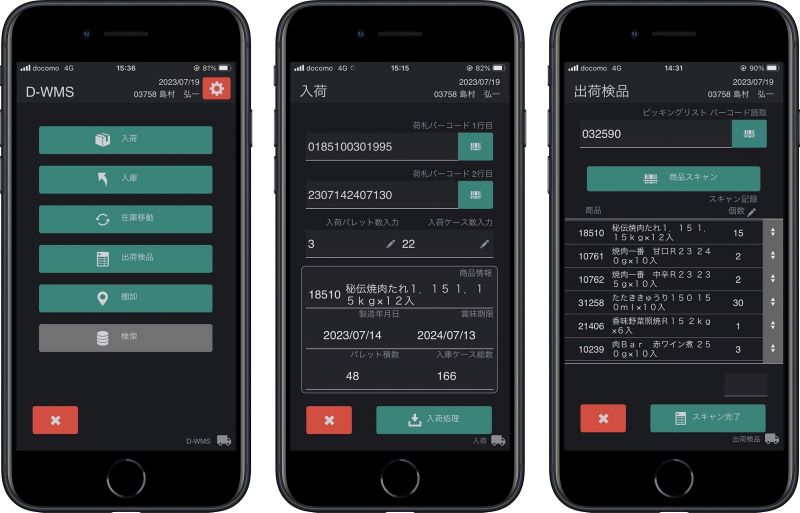
FileMaker Go アプリの画面。入庫や出荷など、一目でわかるレイアウトで直感的な操作が可能
浅美倉庫には 倉庫管理用の iPhone が 8 台用意され、すべてに外付けのバーコードリーダー 「AsReader」を装着している。バーコードや QR コードは iPhone の標準カメラで読むこともできるが、暗い場所で読み取りをする場合も考慮し、より時間を短縮するため外付けのバーコードリーダーを利用することにした。外付けのバーコードリーダーと iPhone の 2 つを合わせても専用のハンディターミナルに比べれば安価だ。
iPhone 上で Claris FileMaker Go アプリ上に構築した 倉庫管理システム「D-WMS」を起動させると、認証が求められ作業者は ID を入力。メインメニューが表示され、入荷・入庫・在庫移動・出荷検品・棚卸の各作業に合わせて利用する。同社の物流部 主任 島村 弘一 氏は、「現場の運用に合わせてアプリ開発してもらったので、使いやすいと感じています。正直、直ぐには馴染めない人がいるかと思いましたが、使えない人は、誰もいない。幅広い年齢層の作業員がいますが、みんな iPhone を使いこなしています」と語る。
「おいしさで・しあわせをつくる」、安心・安全をモットーとする厳密なロット管理
新たに FileMaker を活用して構築した倉庫管理システム「D-WMS」での業務フローを紹介しよう。
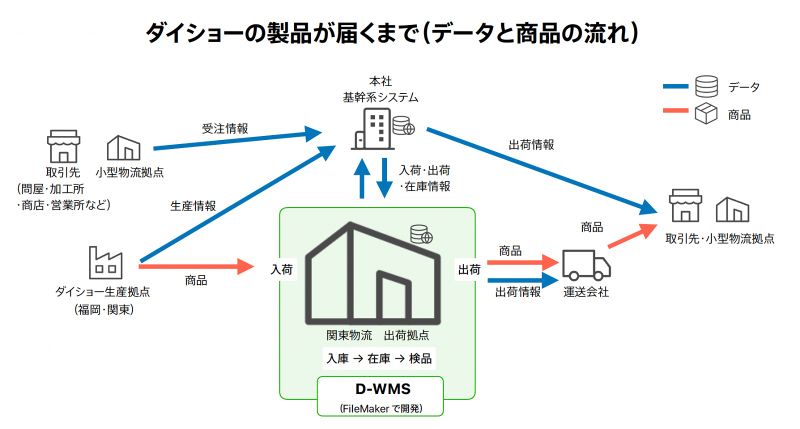
[入荷]工場から商品が届くと、入荷作業を行う。iPhone に装着したバーコードリーダーで伝票を読み取ると、商品コード、商品名、製造日、賞味期限などがシステムに自動で入力される。表示情報と現物を照合し入荷(到着確認)が完了する。が、現場はそう単純でもない。ダイショーが管理する 10t トラック 15 台が工場から配送してくる製品は 540 種類にのぼる。製造日単位でロット分割しているため、1 商品複数ロットのものもあれば 1 商品 8 ロットのものもある。賞味期限が違えば管理も違う。ちなみに、取材当日の倉庫在庫には 1,140 ロットが格納されていた。
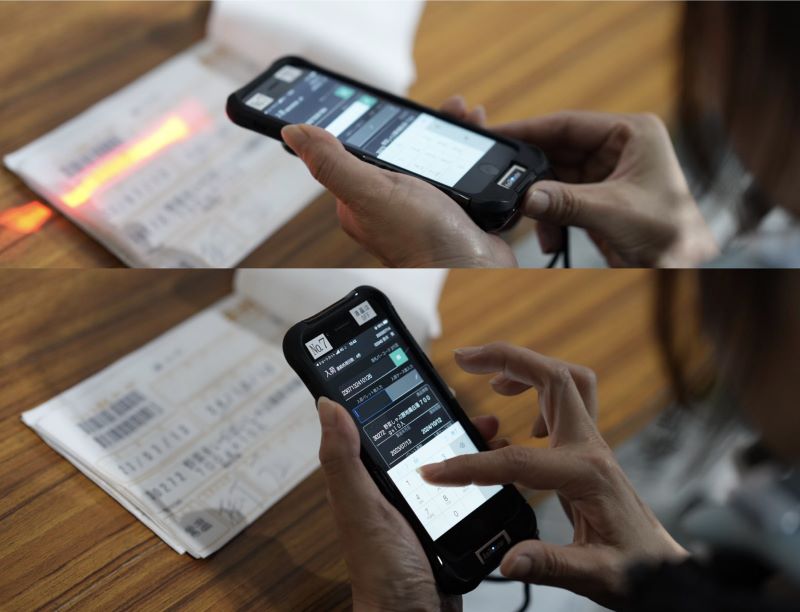
入荷作業の様子
[入庫]次は入荷した商品を倉庫内の適切な場所に納める入庫作業を行う。 入荷した商品のバーコードを読み取って情報を確認し、適切な空きがある場所の棚番号を振り、棚に収納する。
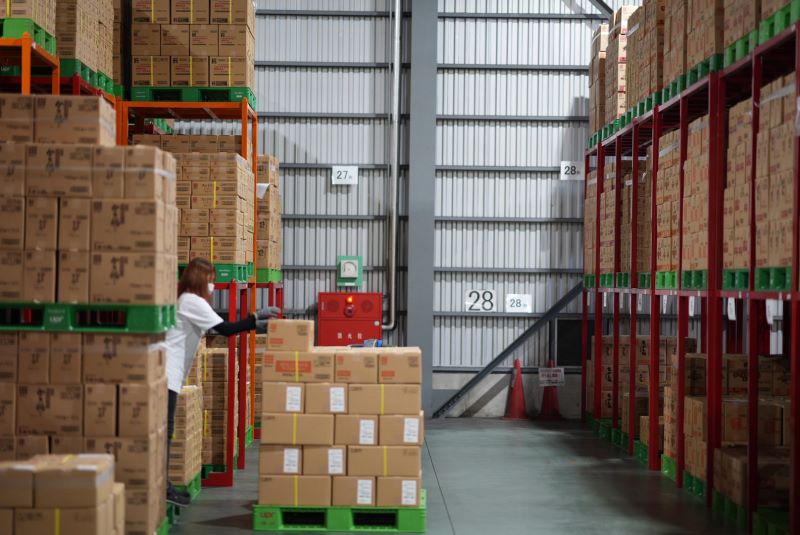
広大な倉庫には列番号が付与され担当者の判断で空いている場所に入庫する
[在庫移動] 入庫時に新たに入荷した同一商品をまとめて棚に納めるため、先に置かれていた小ロットの商品を別のところに移動させた方が効率よく収納できる場合には、在庫移動を行う。これも商品のバーコードを読み取って棚番号を付け替えて移動する。
旧システムではそれらの作業にハンディターミナルを使っており、クレードル経由で同期していた。作業している 8 台のハンディターミナルは、それぞれをいつクレードルにつなげてデータを反映するかわからなかったため、倉庫間移動をしづらかったという。目視と伝票で入荷入力処理していたが、それを反映しないとターミナルからデータを送ることができず、入庫待ちも発生していた。倉庫の面積は約 6,000㎡、 サッカーコート 1 つ分。ハンディターミナルを同期するために頻繁に事務所に戻ることは容易ではなかった。現在、iPhone アプリ D-WMS は 4G/LTE 接続され、データはリアルタイム反映されている。倉庫の人員配置も効率化され、現場の負担軽減につながっている。
[棚卸] 棚卸は倉庫全体で行う。倉庫の基本はパレット(荷物を乗せるための台)単位で管理しており、パレットに搭載する個数は商品梱包のケースサイズ等により決まっているので、パレットを数えれば D-WMS が個数を計算する。旧システムでの棚卸はケース単位で管理しており、都度電卓で個数を計算するため、かなり時間がかかっていた。島村氏は、「開発の段階で個別にお願いした機能の 1 つです。これにより棚卸が格段に速く正確に処理できるようになりました」と評価する。
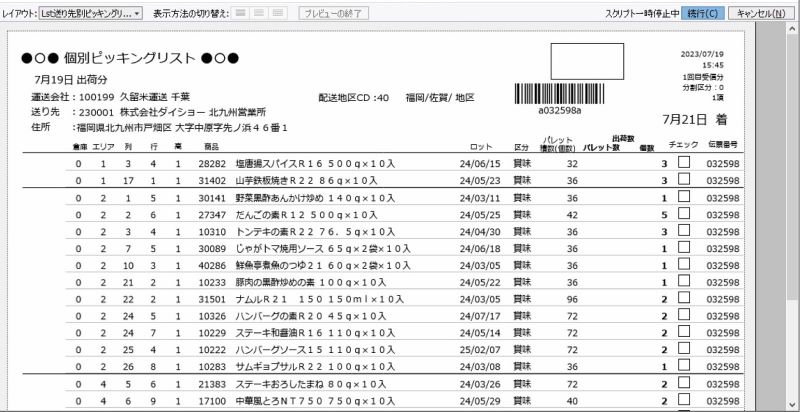
出荷時に紙で運用するピッキングリスト画面は FileMaker Pro から印刷する
[出荷] 出荷時は配送ドライバー向けの帳票や、ピッキング担当者 30 名の作業に必要なため紙の運用を継続しているが、出荷検品では iPhone が活躍する。送り先ごとの伝票に印字されたバーコードを読み取ると、商品コードと商品名が表示されるので、商品数を入力し、指示データと照合。ミスがあれば問題箇所が表示される。島村氏は、「以前は全てを紙でチェックをしていましたが、システム化することで正確性が向上しました」と語る。以前は商品をトラックに積み込んだ後にミスが発覚することがあり、時には積み直しをすることもあった。清水氏は、「旧システムでは積み間違いが起こり、そういうときは 30 分から 1 時間、総出で作業していましたし、ドライバーにも大きな負担となっていました。新システムを導入してから、積み間違いがなくなり効率化につながっています」と語っている。
事務所では、Claris FileMaker Pro (デスクトップ)側の D-WMS でピッキングリストや荷札、送り状などを出力する。iPhone に入力した作業データはすべて PC の管理画面でリアルタイム反映するので、倉庫作業が終了すれば即時締め処理を行い、データを基幹システムに送信して処理が完了する。それによって送り状に関する事務処理、 1 日 40 分かかっていた作業はゼロになった。加えて、運送会社からの仕様変更リクエストであった着店コードの入力などにも対応できるようになった。
ハンディターミナルから iPhone に移行したことで事務所側の作業も大きく削減されたのだ。
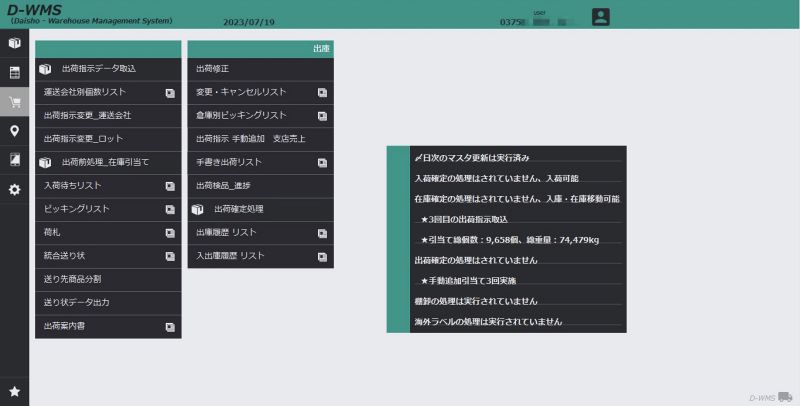
PC の画面では iPhone で行った作業が全て確認できる
FileMaker を軸に、部門間連携へ
社内でシステム開発することに関して物流部の現場を管轄する清水氏は、「以前のようにシステムの改善要望を外部に頼むとお金も時間もかかりますが、社内開発だと現場に来てとことん要望を聞いてくれるのがいいですね」と笑う。要望に応えた松井氏は、「積極的に要望を言ってもらった方が結局良いものにつながりますし、作る方もやりがいがあります」と応える。このチームワークが、同社の FileMaker 活用の根底にある。
情報システム部の加藤氏は、FileMaker を活用した一連のプロジェクトが社内のシステム開発手法の転換期にもなっていると語る。「情報システム部では基幹系システムや全社共通のツールなどを管理していますが、現場の細かい要望にすべて応えるのは難しいのが現状です。そこを現場が FileMaker を使って自分たちで埋めてくれ、助かっています。基幹システムとのデータ連携も当初は不安がありましたが、実際に問題なく運用できています」
今後の FileMaker の活用について三浦氏は、「これまで各部門で活用してきた FileMaker ですが、今後は FileMaker を軸として部門を越えた連携ができないかと考えています。それができれば、DX につながるでしょう」と語る。経営の舵を取る 松本氏も、「FileMaker を活用してシステムを内製化することで、本当に自分たちが求めている業務改善が可能になります。やりがいや達成感、ひいては会社の活性化にもつながります」と評価している。
ダイショーはこれからも FileMaker を活用し、さらなる成果を生み出していくことだろう。
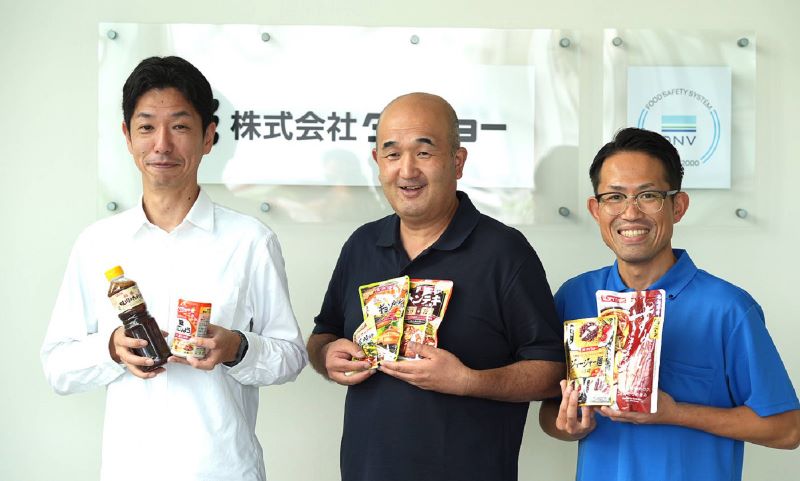
ダイショー関東工場 左から:松井 伸明 氏(経営企画室 部長代理)、清水 良之 氏(物流部 課長代理)、島村 弘一 氏(物流部 主任)
【編集後記】
「味・塩こしょう」や焼肉のたれ「焼肉一番」などの調味料で有名なダイショーであるが、「名店監修鍋」シリーズ、「オートミールde 」シリーズなど次々に新しい味や新商品づくりにチャレンジを続けている。
以前、本ブログでダイショーのアプリ開発事例への取り組みを紹介したが、そこからわずか 1 年。これほどの短期間で、ハードウェアを含めて大がかりなシステムを成功させた例は珍しい。そのうえ、システム面でも新アプリづくりにチャレンジを続けている。製造業 DX に取り組むにあたって、大手システム開発会社やコンサルティング会社に頼っている企業が多いなか、ダイショーは社員の人材育成を推進し、DX への取り組みを加速している。それを実現した根底には、社員のコミュニケーションが活発で、和気あいあいとしたダイショーの企業風土もあるのだろう。自由に意見が言える雰囲気と、挑戦と失敗を許容する包容力が、開発力と提案力を高め、社員の挑戦する姿勢を育んでいるのではないだろうか。
*QR コードは株式会社デンソーウェーブの登録商標です。