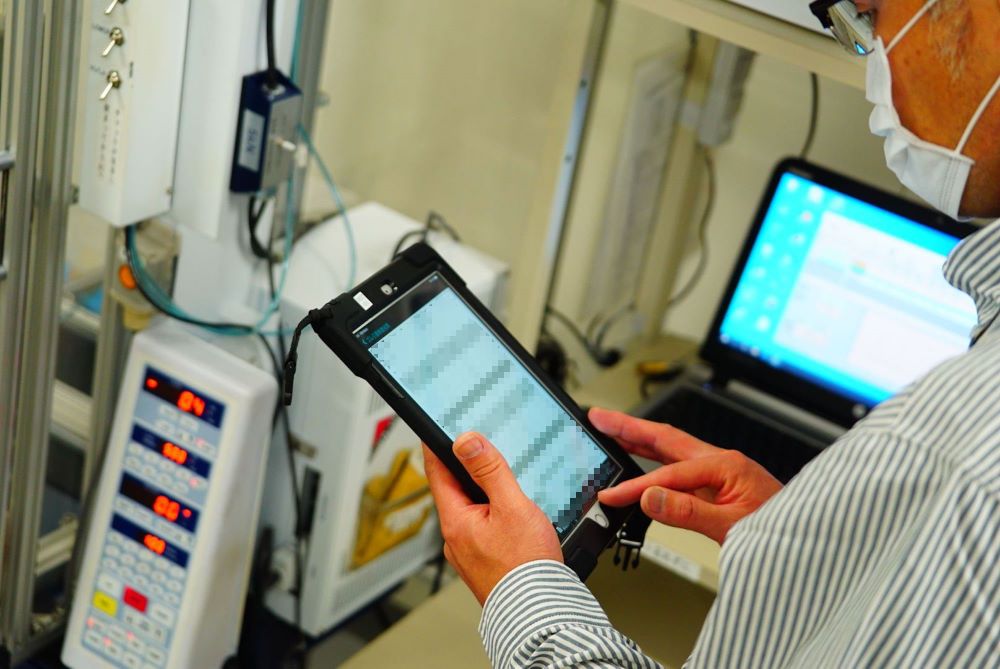
株式会社ブリヂストンは 1931 年に設立され、今や世界 150 か国以上でビジネスを行っているタイヤ・ゴム業界におけるグローバルリーディングカンパニーである。乗用車、バイク、航空機、産業用車両、建設・鉱山用車両にいたるまで、ありとあらゆる運搬の安全を支えている。
1968 年に制定された社是「最高の品質で社会に貢献」は今なお世界中の従業員一人ひとりに受け継がれており、その使命を大前提とし「社会価値・顧客価値を持続的に提供するサステナブルな会社」を中長期事業戦略構想のビジョンとして掲げている。
品質はお客様の安全と満足度向上のために不可欠なものと考えるブリヂストンでは、「品質宣言」は、製造だけでなく全てのバリューチェーンの業務品質と、そのアウトプットとしての全製品・サービスの品質を対象としている。品質意識の浸透と、品質活動のレベルアップを図ることを目的として、ブリヂストングループ・グローバル TQM(Total Quality Management)大会が開催され、2019 年の大会には世界各国から 約 270 人の従業員が参加。約 4,500 件もの事例の中から各事業所で選ばれた 16 件の改善事例が発表され、その TQM の取り組みはコロナ禍においても継続的に行われている。
1938 年 7 月に国内工場としては 2 番目に操業開始した横浜工場では、現在コンベヤベルト、免震ゴム、防振ゴムなどタイヤ以外のゴム関連製品などを扱っている。今回のインタビューでは、主に鉱山などで鉱石や石炭、土砂などを輸送する設備に使用されるコンベヤベルトの品質保証を担当する 横浜工場品質保証課 竿田 健さんと 検査係 上村 力さんに品質管理に取り組む姿勢と、データ管理向上への取り組みについてうかがった。
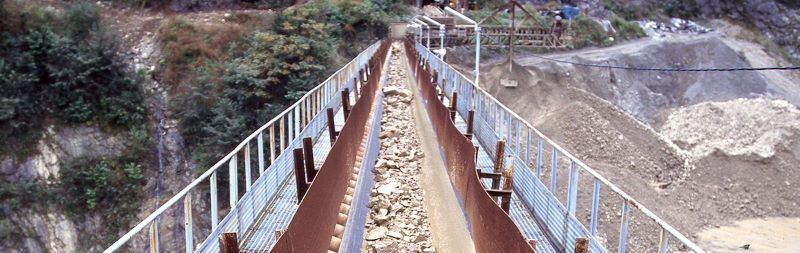
鉱山で利用されるコンベヤベルト
鉱山のオペレーションに必要なソリューションを提供
ブリヂストンでは、鉱山での運搬において故障によるダウンタイムを排除するため、様々なサービスを組み合わせて現場密着型ソリューションを提供している。その一つの役割を担うのがコンベヤベルトだ。鉱山などで鉱石や石炭、土砂などを輸送するコンベヤベルトは、耐久性、耐熱性などの確保に高い技術が用いられている。
コンベヤベルトの操業において発生するエネルギーロスについては、ベルトがローラーを乗り越える際に発生する抵抗(ローラー乗り越え抵抗)が最も大きいことに着目し、低燃費タイヤ「エコピア」で培ったゴム材料開発技術を応用し、省エネルギー性能を追求したコンベヤベルトなどを全世界に出荷している。
「コンベヤベルト」と一口に言っても、出荷する製品は耐摩耗、耐熱、耐衝撃、耐油、傾斜輸送、難燃、耐薬品など、運搬用途によってさまざまだという。幅や長さの仕様も多様であるため、大半は納品単位でカスタマイズする特注品となる。どのような用途で使われるにせよ、決して運搬を止めないためのソリューションを支えているのが、品質検査に合格した製品である。
コンベヤベルトの検査項目は複数あるが、品質保証課では主に物性検査を行っている。
たとえば、耐摩耗性検査では、円筒状のサンプルをサンドペーパーをまきつけたドラムに一定荷重でおしつけ、ドラムを回転しながら試料を一定距離走行させた時の摩耗量を測定する。他にも、破断するまでサンプルを引っ張り、強度と伸度を測定する引張検査や、サンプルを燃やして難燃性能を測定する燃焼検査などがあるが、検査で最も重要なのは、検査データを正しく合否判定することである。
アジャイル開発の真髄 現場と開発者の協業
これまで検査データは全て紙に印刷、その内容を PC にインプットして合否判定を行い、最終的に上長が承認したうえで、検査成績書にまとめてお客様に提供していたが、検査結果が出るまで、長いものだと数週間を要する場合があり、これらのデータを紙で複数の担当者が内容を把握するには、相当な管理の手間が発生すると同時に、同じファイルを複数名で閲覧できない、承認回覧に時間を要する、紛失リスクなどの問題もあった。
そこで品質保証課 竿田氏は、電子化への取り組みの検討を開始した。当然ながらコンベヤベルトに使われる検査システムの既成パッケージなどは存在しないうえ、お客様によって複雑な検査内容によるカスタマイズが入るため、システム導入は単純な要件定義ではない。そこで他部門に相談したところ、ブリヂストンでは既にアジャイル開発プラットフォームとして Claris FileMaker の導入実績があることがわかった。製造設備点検の部門でも FileMaker は使いやすいとの社内評価があり、社内で紹介を受けた Claris FileMaker の 認定パートナー 株式会社イエス ウィ キャン(以下、YWC 社)に開発を委託。要件定義の策定に取り掛かった。
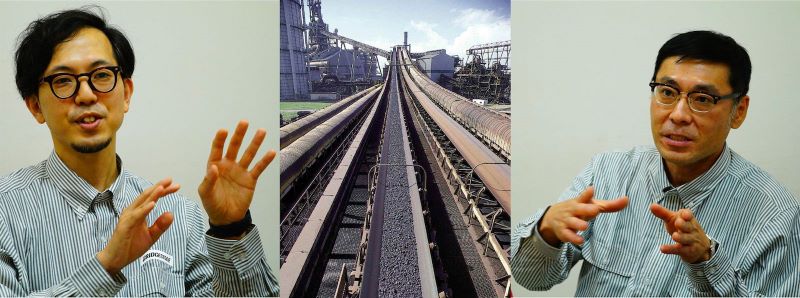
左:品質保証課 竿田 健さん 右:品質保証課 検査係 上村 力さん
YWC 社の数あるプロジェクトの中でも、今回の検査システムは異例中の異例。というのも、お客様ごとで納品が異なるものづくりの最終工程である品質管理の検査は、そのフローが固定化されているわけではない。職人気質を含めて熟練の経験と知識が要求されていた。
例えば、どの素材のどの用途であれば、どのような検査が必要で、どの検査が不要になるか、そしてそれに伴う高品質を保証するしきい値はどの値であるべきかといった要件がある。同社でシステムコーディネーター(お客様と開発部門の橋渡し役)を担う芳野 由喜子氏は、「検査の仕組みを理解するのにかなりの時間が必要でした。実際に現場を見学させていただき、どのようにシステムに落とし込んでアプリで動かしていくのか、テストの繰り返しでした。仕組みと器を用意するのは開発の仕事ですが、規格をマスタ化していく作業は現場の方の努力が必要です。検査係の上村さんのマスタ作成作業があったからこそプロジェクトが完了できたといえます」と現場と開発者が一体となったアジャイル開発の成功を語る。
竿田氏によると今回のシステムリリース後、改修は一切発生しなかったという。というのも、品質保証課の現場担当者と、YWC 開発担当者との間で何度もテストを繰り返し、100 点満点で納得できる状態にしてからリリースしたからだ。品質保証課の最終アウトプットとなるお客様が受け取る検査成績書は、ミスが許されない世界。ブリヂストンの社是「最高の品質で社会に貢献」は、たしかに社員全員の頭の中にインプットされていた。
QR コードを活用して紙から iPad へ
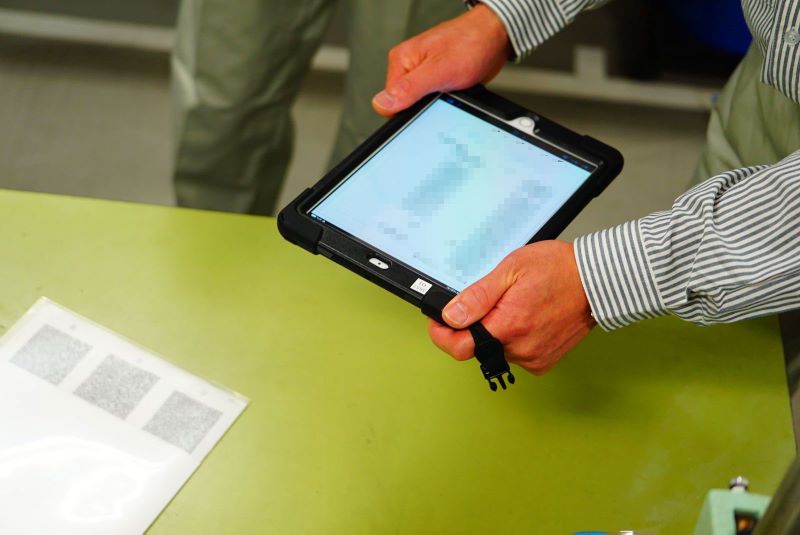
検査サンプルの QR コードを読み取ると、検査する製品に合わせた画面が表示される
見た目は同じコンベヤベルトでも、熱に強い、油に強いなど仕様は様々で、お客様の要望する製品仕様により検査項目が複数ある。多様な検査をシステムに反映させるため、検査項目をどのように組み合わせるのか、社内の専門用語をシステム開発者に伝え、システムとして可視化して、アプリとしてリリースするまでに約 1 年の期間を費やした。
検査の際は iPad を使用する。製品ごとに異なる検査項目を間違いなく iPad 上で入力できるよう、検査開始時に iPad 上の FileMaker Go アプリから 検査サンプルの QR コードを読み込ませる。すると、その製品に必要な検査項目だけが画面上で操作できるようになる。
一部の検査データは検査機器からファイルサーバーを経由して iPad にインポートされ、検査完了後は、設定された計算式が処理され自動で合否を判定。データはロックされて更新できないようになっている。ワークフロー形式で上長が自動判定された検査合格を最終確認し、お客様に提出する検査成績書をアプリ内で自動発行することもできるようになった。
現場では FileMaker で作成された検査状況を大型モニターに表示させ、複数人で検査進捗を管理している。

検査室内に設置されたモニターで検査の進捗が確認できる
属人化の排除へ向けて
今回のシステム化でアプリの機能として導入された「検査前チェック」は、検査をする前に、チェックすべき項目、検査機器に入力すべき値、間違いやすい項目の注意喚起など、これまで上村氏をはじめとした検査担当者の頭の中にあったノウハウを洗い出したものである。これにより、人によってどうしても発生し得るバラツキを排除することができた。徹底した検査体制が、システム導入によってより万全なものになったと言える。
また、システム化の過程で、現場を知らない社外のシステム開発者に説明しながらアジャイル開発でプロジェクトを進めたことが、結果的に業務プロセスの見える化につながった。ブリヂストンでは、一人ひとりが複数の工程を遂行できる多能工化の取り組みを以前から行っていたが、「検査前チェック」をはじめ、属人的な「勘・コツ」を見える化できたポイントは大きい、と竿田氏は語る。この成果は、今後の後輩育成や、デジタル人材の育成にも貢献していくであろうと竿田氏は期待を寄せている。
【編集後記】
取材の際、品質保証課 検査係の方々が日々働く現場を見学させていただいた時に目に飛び込んできたのは、数々の備品の定位置を示すテープマーカー、工場内の横断歩道を渡るときに行う指差し安全確認、あるべきものがあるべき所に必ずあり、安全を意識し続けるという愚直なまでに基本に忠実な製造の現場だった。
単なる”モノ” を作って売る会社ではなく、高付加価値品を生産販売するブリヂストンの強さの秘密は人にあると感じた。そのブリヂストンの現場が取り組んだアジャイル開発は、通常は起こりえるはずの開発後の手直しをゼロにするまで追求する精神、まさに「最高の品質で社会に貢献」が 滲み出る開発プロジェクトだったといえる。
昨今のアジャイル開発とローコード開発の組み合わせにおいては、プロジェクト進捗と早期着手が重要視され、走りながら完成を目指す開発案件が増えている中で、お客様重視でブレのないアジャイル開発を実現した株式会社ブリヂストン。社員の方々のこだわりに改めて学ぶところの多いインタビュー取材となった。